Battery Thermal Management System plays a crucial role in Electric Vehicles. EV’s have transformed the automotive industry, providing a more sustainable alternative to traditional internal combustion engines.
At the heart of this revolution is the EV battery, a critical component that powers the vehicle and directly impacts its performance, range, and safety. Understanding the importance of EV batteries and the role of Battery Thermal Management Systems (BTMS) is essential for both current and future EV technology.
This article discusses Battery Thermal Management Systems and their importance in the EV world.
Importance of Battery in an EV
The EV battery serves as the power source for the vehicle’s electric motor, converting stored chemical energy into electrical energy for functioning.
Here’s why the battery is so crucial,
Energy capacity of the battery, measured in kilowatt-hours (kWh), determines how far an EV can travel on a single charge. Higher capacity batteries offer longer ranges, making EVs more practical for daily use and long trips significantly reducing range anxiety.
The battery’s power output affects the vehicle’s acceleration and overall driving performance. A high-performance battery can deliver the necessary power for rapid acceleration and high speeds.
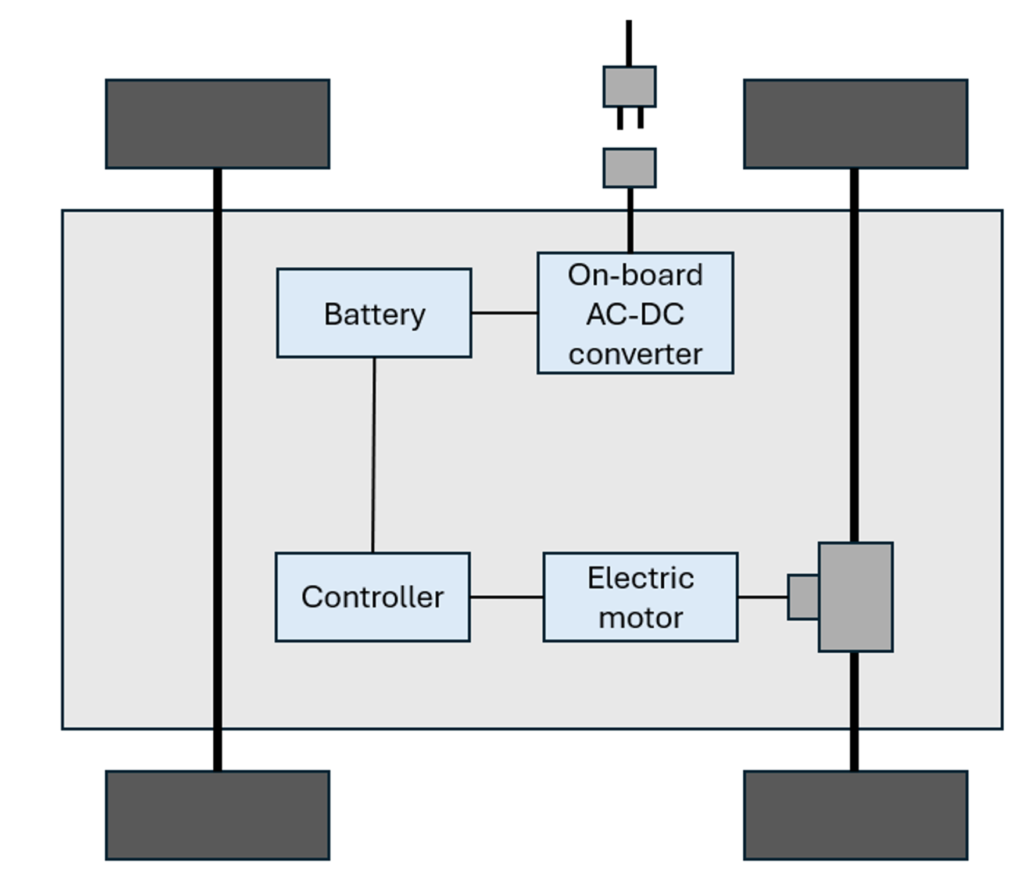
Battery efficiency influences the overall energy consumption of the vehicle. Advanced battery technologies improve gravimetric energy density (kWh/kg), leading to better performance and longer range.
NMC or LFP, which is the Better Choices for Electric Vehicles?
NMC cells are composed of Nickel, Manganese, and Cobalt in various ratios (Refer fig: 2) and provide a balance between energy density, power density, and cycle life. And in general, NMC has higher energy density (150-220 Wh/kg). LFP is Composed of Lithium Iron Phosphate, also LFP has a stable chemistry. But LFP has lower energy density (90-160 Wh/kg).
In terms of cycle life NMC has good cycle life but tends to degrade faster than LFP under high stress or fast charging conditions. LFP cells generally have longer cycle life and better thermal stability. It can handle more charge and discharge cycles before significant capacity loss.
Which is Best?
While talking about safety NMC cells are generally safe but can be prone to thermal runaway if damaged or improperly managed and the presence of cobalt and nickel can increase the risk of thermal instability and safety. It is less likely to catch fire or explode, even under extreme conditions.
Their electric counterparts, which emit no tailpipe emissions, provide a significant environmental benefit. However, the success of these EVs hinges on the efficiency and convenience of their charging infrastructure
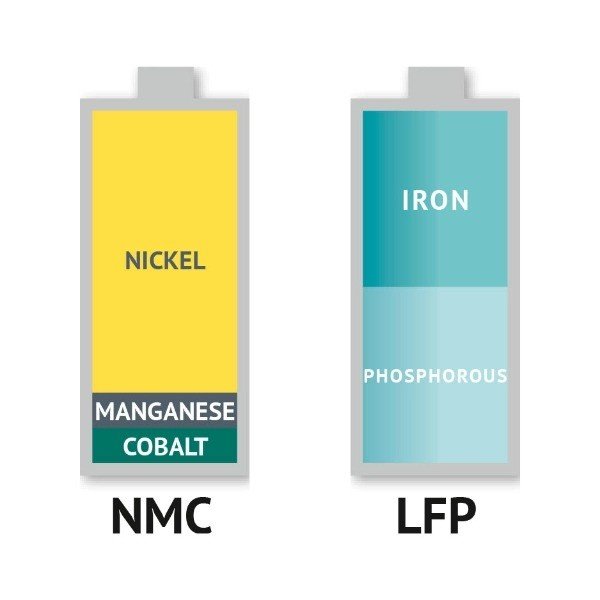
On the other hand, LFP cells are known for their excellent thermal stability and safety. It is less likely to catch fire or explode, even under extreme conditions. Coming to economy, cost of NMC cell is higher due to cobalt and nickel. Whereas the cost of LFP cells is lower due to using more abundant and cheaper iron.
In conclusion LFP batteries are preferred for applications where safety, cost, and cycle life are prioritized over energy density. They are more durable and cost-effective but have lower energy density and power output compared to NMC.
Why do EV Batteries Need Battery Thermal Management Systems?
EV batteries need to operate optimally within a specific temperature range. Extreme temperatures, both high and low, can negatively impact battery performance and longevity. Lower temperatures result in sluggish performance of the battery, while higher temperatures accelerate the cell degradation.
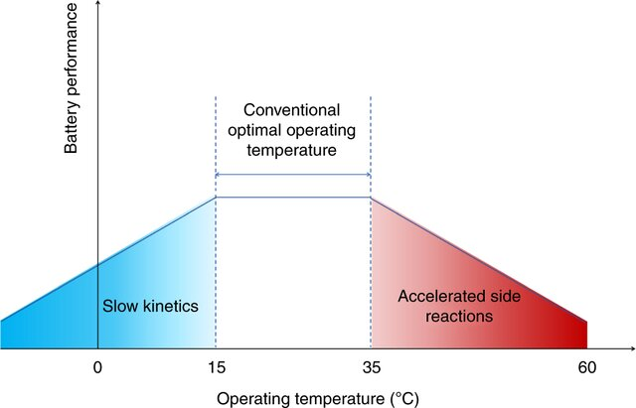
The process of generating heat in a conductor or resistive material when an electric current flows through it, due to the material’s electrical resistance is called Ohmic heating. Thus, heat is produced while charging and discharging the battery.
This is where Battery Thermal Management Systems (BTMS) come into play. BTMS plays a critical role in managing the heat generated by ohmic heating, ensuring efficient operation, safety, and longevity of battery systems in electric vehicles and other applications.
What Can a Battery Thermal Management System Do?
1. Temperature Regulation: BTMS uniformly maintains an optimal operating temperature of all cells across the battery pack. This is crucial for ensuring consistent performance and extending battery life.
2. Safety: Overheating can lead to thermal runaway, a dangerous condition that can cause fires or explosions. BTMS prevents overheating by cooling the battery when necessary.
3. Performance: Temperature fluctuations can affect battery efficiency and power output. A well-managed temperature helps maintain the vehicle’s performance and range.
4. Longevity: Prolonged exposure to extreme temperatures can degrade the battery’s chemical components, reducing its lifespan. BTMS helps in maintaining the battery’s health over time.
Types of Battery Thermal Management Systems Available
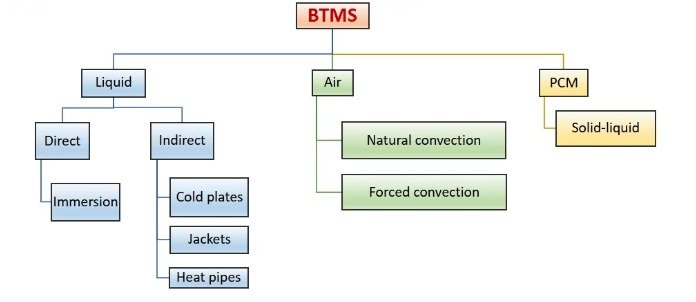
There are several types of Battery Thermal Management Systems, each with its own advantages and applications:
1. Air-Cooled Battery Thermal Management System
This system uses air to dissipate heat from the battery. It is simple and cost-effective but may not be able to maintain the temperature of the battery pack within limits during rapid charging/ discharging of the EVs.
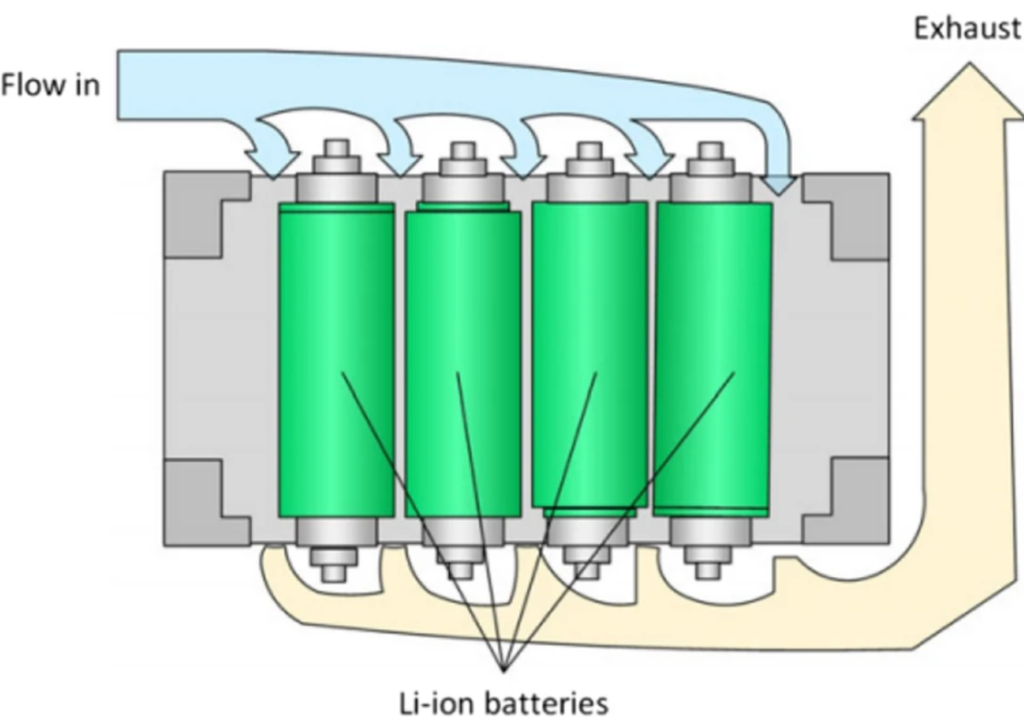
Air Cooled BTMS is of two types viz. Active and Passive Air cooled BMTS.
Active Cooling uses fans to force air through the system actively. Passive cooling relies on natural convection to dissipate heat without using active components. This is often used in systems where cooling demands are less intense.
2. Phase Change Material (PCM) Based Battery Thermal Management System
PCMs absorb and release heat as they change states (from solid to liquid and vice versa). This system can provide temperature stability but may be less effective than liquid cooling. Unlike air cooled and liquid cooled BTMS, this technology is still evolving and has not been commercialized.
3. Liquid-Cooled Battery Thermal Management System
This system uses a liquid coolant to move heat away from the battery and dissipate into the surroundings. It is more efficient than air cooling and is often used during rapid charging/ discharging of EVs. In Flextron, our FlexSatck battery pack is built with liquid cooled BTMS.
Types of Liquid Cooled BTMS
Liquid cooled BTMS are of different types. The main types are as follows,
Direct Liquid Cooling
Direct liquid-cooled Battery Thermal Management Systems (BTMS) use liquid coolant to directly contact the battery cells or modules, providing efficient heat dissipation and temperature regulation. Direct liquid cooling provides efficient heat removal directly from the battery cells.
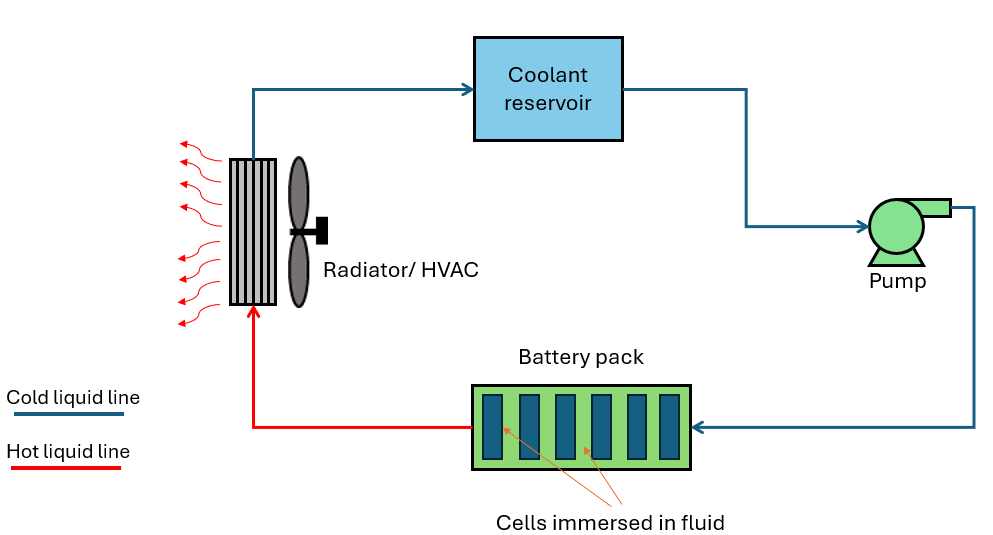
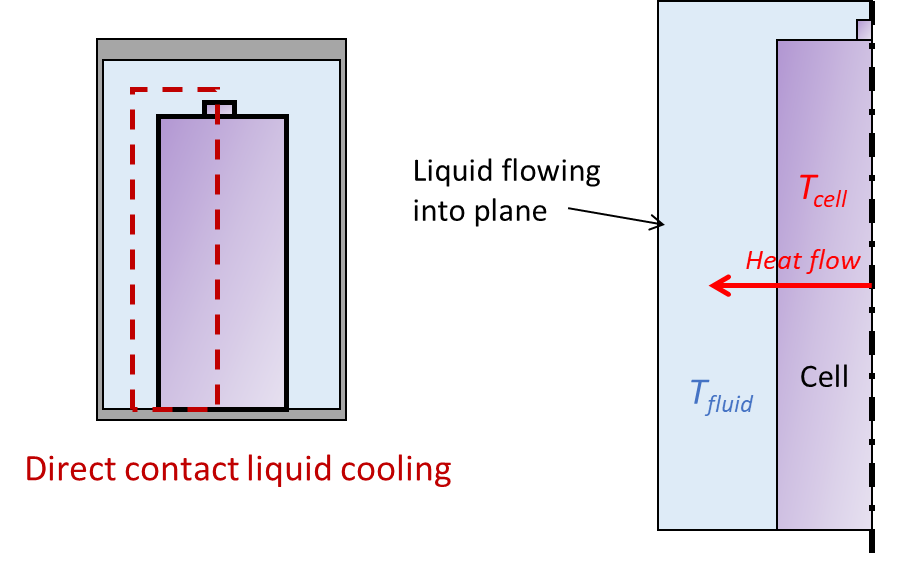
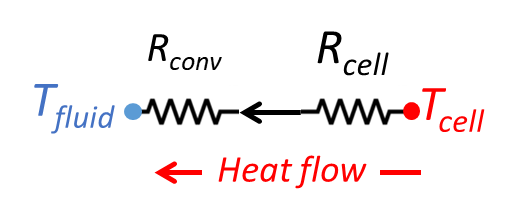
Desirable properties of an immersion cooling liquid
A suitable immersion cooling liquid should have the following properties:
- Electrically insulating/non-conducting: To prevent short circuiting
- High specific heat: To achieve temperature uniformity
- High thermal conductivity: To lower thermal resistance
- Non-flammable: To reduce fire risk during thermal runaway
- Low viscosity: To reduce pumping power
- Chemically inert: To avoid unwanted chemical reaction with cell material
- Low density: To reduce overall weight of the battery pack
Suitable candidates: Dielectric fluids such as silicone oil, transformer oil, hydrofluoroethers, etc.
The Direct liquid cooled BTMS further divides into Active and Passive Cooled BTMS.
Active Cooling uses pumps to circulate the coolant through the system actively. Mainly used in systems where rapid changes in temperature need to be managed effectively.
Passive cooling relies on natural convection currents developed in the fluid within the battery pack due to temperature gradient to dissipate heat without using active components. This is often used in systems where cooling demands are less intense or where cost and complexity need to be minimized.
Indirect Liquid Cooling
The coolant circulates through a separate cooling plate or heat exchanger that is in thermal contact with the battery pack but does not flow directly over the battery cells and does not have direct contact with the cell.
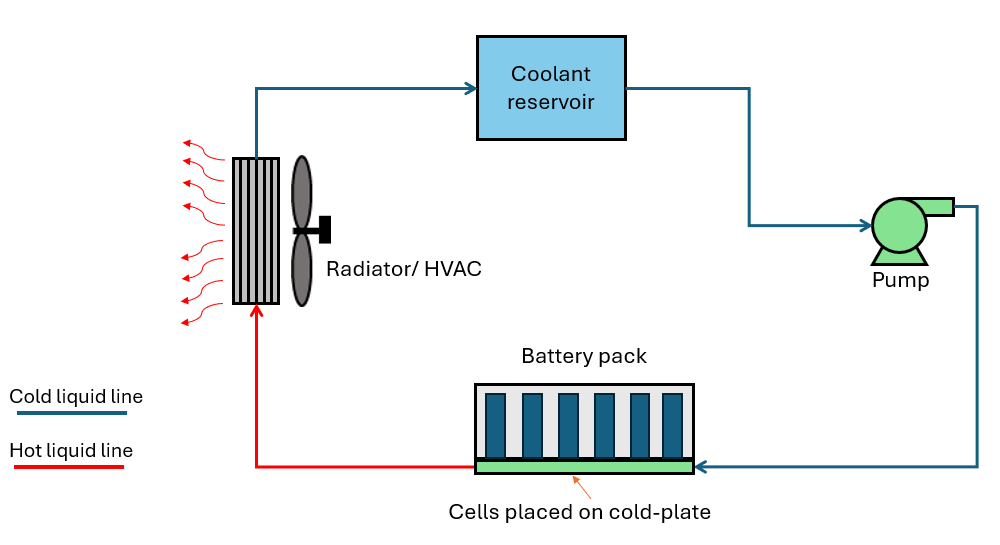
This is simple in design with low maintenance compared to direct cooling and has been implemented commercially. As the coolant is not in direct contact with the cells, water-based coolants can be used in this type of BTMS.
Suitable candidates: Water, water + glycol mixture, etc.
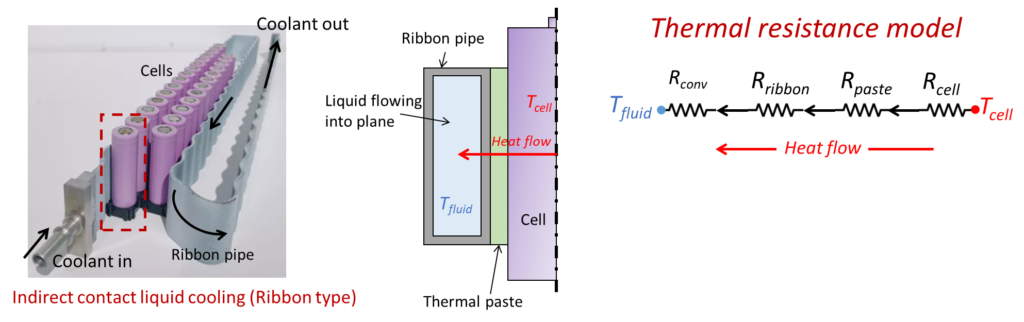
Dual-Loop Cooling Systems
Since the Dual Loop method optimizes the overall system performance and efficiency this is used in advanced EVs and high-performance vehicles where multiple cooling needs to be managed.
Each type of liquid-cooled BTMS has its own advantages and is chosen based on factors like cooling efficiency, system complexity, cost, and specific application requirements.
Why EVs are Shifting Towards Liquid Coolant for Battery Thermal Management System
Liquid coolant systems are becoming increasingly popular in EVs for several reasons. The one main need for EV’s to have BTMS is Fast and Rapid charging.
Conventional charging times for existing EVs (India)
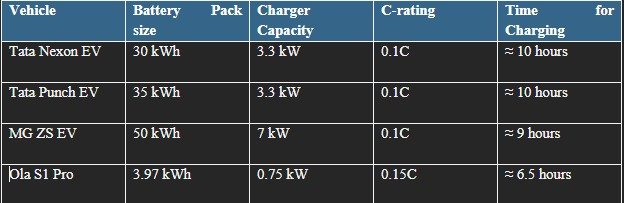
The existing charging infrastructure supports 0.1C-0.25C rating, indicating a charging time of around 10 hrs. and 6 hrs. for 4W and 2W, respectively. Unlike refueling of ICE vehicles, charging time of an EV is significantly longer that prevents the mass adoption of EVs.
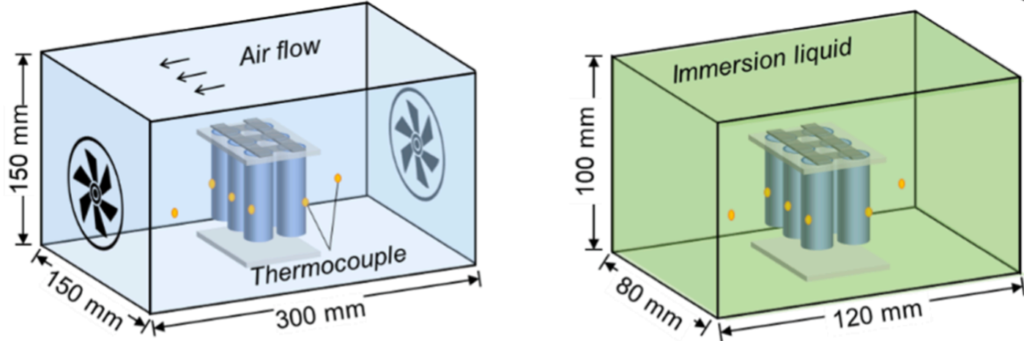
Also, fast charging generates significant heat due to high current flow and ohmic heating in the battery cells. To charge EVs in 15 mins, a battery pack should be charged at 4C rating, which leads to an increase in heat generation by 256 times than the conventional charging. Existing air-cooled BTMS are incapable of removing heat generated during rapid charging of a battery pack. Thus, liquid based BTMS is required to manage and dissipate this heat to prevent overheating.
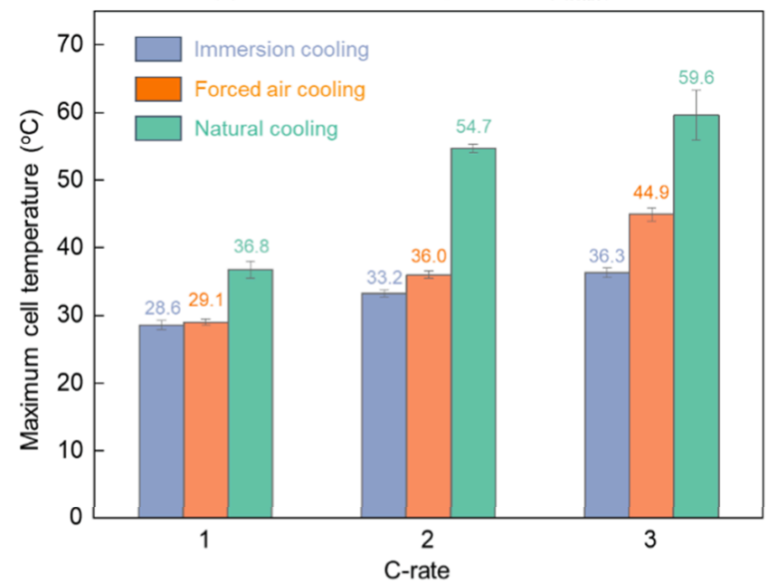
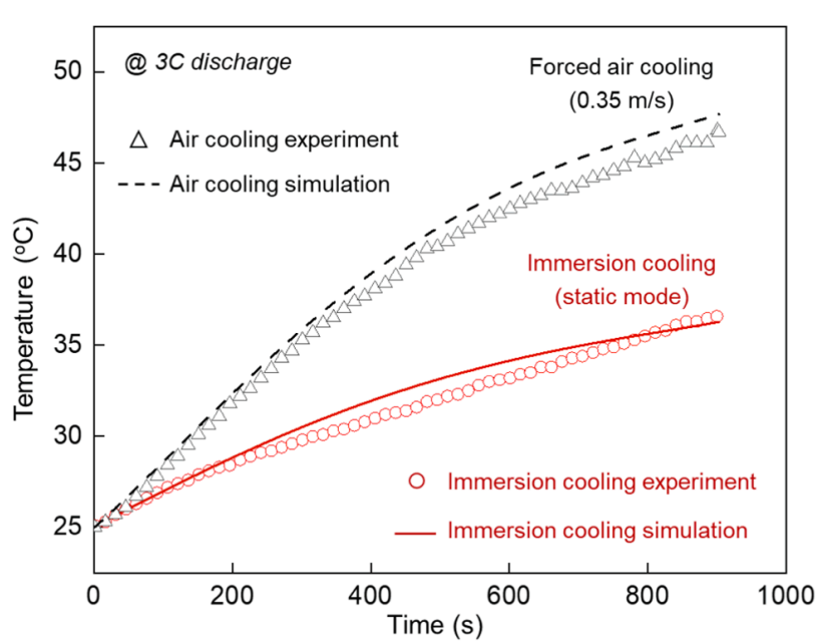
Few other reasons are as follows,
1. Efficiency
Liquid coolants have a higher thermal conductivity compared to air, allowing for more efficient heat dissipation. This is crucial for maintaining battery temperatures within safety during fast charging/ discharging of the battery pack.
2. Performance
Liquid cooling systems can handle and dissipate higher heat loads, making them suitable for rapid charging/ discharging of EVs.
3.Compact Design
For EVs that can support rapid charging, liquid cooling systems can be more compact and lightweight compared to air cooling systems. This is beneficial for space and weight constraints in EV design.
4. Temperature Control
Liquid cooling provides uniform and precise temperature control, ensuring that the battery operates within its optimal range.
Still liquid coolant method has its own disadvantage such as need of more components in the system, regular maintenance etc.,
5. Safety Against Thermal Runaway
Improving the cooling rate of a battery pack helps confine and mitigate thermal runaway by efficiently managing heat buildup. By enhancing heat dissipation through advanced cooling methods like liquid cooling, the thermal runaway is confined to a certain region and other cells in the battery pack are blocked from high temperatures eventually reducing the risk of catastrophic failures.
Conclusion
The EV battery is a critical component that impacts the range, performance, and cost of electric vehicles. Battery Thermal Management Systems (BTMS) are essential for maintaining optimal battery temperature, ensuring safety, and prolonging battery life.
As EV technology advances, the shift towards more efficient and precise cooling methods, such as liquid coolant systems, highlights the ongoing efforts to improve battery performance and vehicle reliability.
Air-based BTMS is ineffective at higher charging/ discharging rates, hence necessary to implement liquid-based BTMS. Dielectric fluids such as silicone oil, transformer oil, hydrofluoroethers, etc. are used as an immersion fluid.
The type of immersion cooling to be implemented in a pack strongly depends on multiple factors viz. charging/discharging rate, volume & weight budget, ambient conditions. Understanding these systems helps appreciate the complexity and innovation behind modern electric vehicles.
Visit: Flextron to know more about our Battery packs.
References
- Sun, X. et al. (2019) Technology development of electric vehicles: A Review, MDPI. Available at: https://www.mdpi.com/1996-1073/13/1/90 (Accessed: 05 August 2024).
- John (2024) ‘LFP vs. NMC Battery: What is the Difference?’, Ufine Blog, 17 April. Available at: https://www.ufinebattery.com/blog/lfp-vs-nmc-battery-what-is-the-difference/.
- Fayaz, H. et al. (2021) ‘Optimization of thermal and structural design in lithium-ion batteries to obtain Energy Efficient Battery Thermal Management System (BTMS): A critical review’, Archives of Computational Methods in Engineering, 29(1), pp. 129–194. doi:10.1007/s11831-021-09571-0.
- Liu, Yanhui, Gulzhan Aldan, Xinyan Huang, and Menglong Hao. “Single-phase static immersion cooling for cylindrical lithium-ion battery module.” Applied Thermal Engineering 233 (2023): 121184.
About Author
Ajinkya Sarode (PhD) is working as a Thermal Dynamics Engineer at Flextron. His expertise spans thermal management of Li-ion battery packs, fuel cell systems, and hydrogen production from methane and methanol.
Moreover, his dedication towards R&D has been reflected in numerous publications in peer-reviewed international journals.
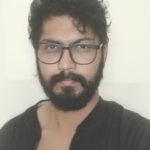